Emerging Automation in the Coal Mining Industry You Need to Know About
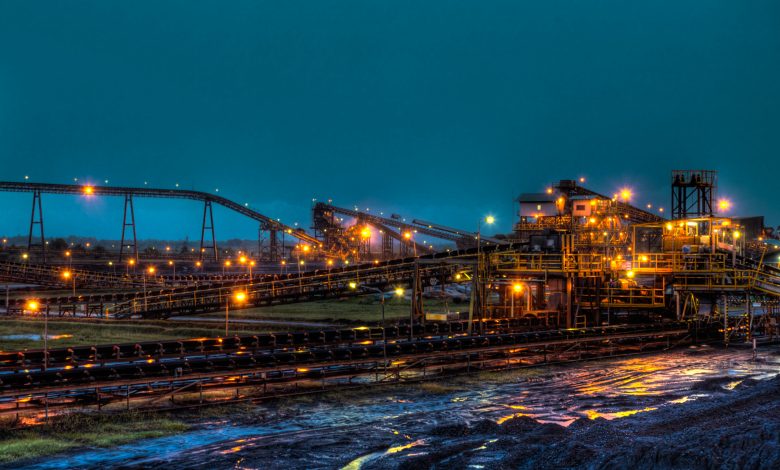
Coal mining has always been a time and labor intensive process. Add to it the processes of refining and processing of coal, and you have a highly energy draining process at your hands that requires way too much capital and way too many workers. Over the past several years, many innovations have led the way for top notch machineries that have allowed the coal mining industry to breathe an air of respite. This has solely been credited to hands-on research and development of advanced technologies.
Gone are the days when miners used pickaxes, oil lanterns, and other hand held tools to go underground and mine manually for days at a stretch. In fact, most coal mines don’t even require workers to go deep under the ground. Thanks to the sophisticated automation solutions that are used to plan and design mining fields, blast sites, and more. Here, automated machineries and vehicles are sent to carry out the process of mining in lesser time.
Revolutionary Changes in the Coal Mining Industry Over the Past Several Decades
The coal mining industry operates in a way such that it has and continues to put a lot of pressure on the environment. It has utilized vast resources of energy, water, machineries, human labor, and more, and many a times, it has uprooted tribal settlements near the mining area, making them homeless. The tremendous social, economic, and environmental pressure exerted by the coal mining industry over the past several decades has forced it to change the way it operates and approach mining with a much more safe and sustainable way.
With time, the advanced technologies have also paved the path for automated technologies that have further helped the industry to reduce the need for a large workforce and a huge capital. The main idea of introducing automations in the coal mining process was to primarily eliminate the need for human labor and increase productivity. This has ultimately led to faster and more efficient mining processes.
It’s important to note that, in developing countries, where the cost of labor is very low, the introduction of mining automations only serves the purpose of eliminating the need for human labor and increasing productivity and doesn’t help to reduce the amount of investments made. This is because the incentives earned for increased productivity and efficiency are quite minimal. Automations in the coal mining industry can be applied to two major areas:
- Automation in process
- Automation in software
These automations have started making a place for themselves in the industry; however, they are still in their transition phase. It’s still a long way to go for the entire coal mining process to become completely automated. Read on to understand what have been the recent emerging automations in the coal mining industry.
Automation in Machinery

Driver Assist Automations
The terrain where coal mining takes place is incredibly rough and risky. In addition, you need a lot of heavy machinery to navigate through the terrain well and carry out mining operations seamlessly. This requires drivers of bulldozers, excavators, and other heavy machinery to be extra careful. They need to be trained well to be able to drive on such rough terrains, where a single mishandling could lead to damage to property and loss of lives. Advanced technology has allowed such heavy machineries to be equipped with driver assist automations just like the ones we have in our cars.
The spotting assist feature allows the mining machine drivers to avoid any obstacle in their path. In addition, the collision avoidance systems alert the driver about the proximity of obstacles, such as boulders and sharp objects. Putting the machine in reverse and moving back and forth on bad trails have been made very easy with such driver assist features. Currently, some machines also provide driving assistance features that allow the drivers to take care of things in their blind spots.
Remote Control Automations
Remote control automations take it a whole step further by allowing mining machine drivers to control the machinery from a distance with the help of a remote control device. They can stand in the line of sight of the complete landscape and control numerous pieces of mining equipment, such as excavators, large drills, bulldozers, loaders, dumpers, graders, and rollers, from a remote location. While these remote control automations allow the drivers to control the operations of the mining equipment from a distance, it reduces the productivity. This is because it can get difficult to handle the equipment from such a long distance without getting the feel of what you are driving around.
However, the main application of remote control automations is in scenarios where the situation is incredibly dangerous for people to go in, such as fallen debris, unstable or sinking terrain, high risk areas, and underground mining.
This allows miners and engineers to carry on with their regular operations even in high risk areas. They don’t have to lose out on abundant reserves and deposits of coal simply because they are facing risks to machinery and human lives. In short, miners, engineers, and machinery handlers can now stand away from the risky areas and still dig to get out to coal reserves. To add on, these controlled automated mining machineries are pretty affordable.
Teleoperated Mining Automations
Going another step further, we have teleoperated mining equipment. Miners and engineers can now choose automated machineries that allow them to carry out the mining operations while being miles away from the actual site of mining. Cameras, sensors, positioning devices and software, mirrors, and more are used to view the entire area that needs mining. Controlling devices for these equipment include joysticks, hand held controls, and more. Research is also ongoing about how these mining operations can be carried out by using remote devices, such as desktops, where a particular action can be triggered with a single touch on the screen.
Teleoperated mining automations offer a better vantage point and control than those offered by remote control automations. Since positioning devices and software are used, the handling of things gets much easier; however, it does take a little more time to get better results. These automations are highly useful when you need to dig underground in extremely confined areas, where the entry of humans can be a huge risk to their lives.
Full Automations
By fully automating the mining equipment, the human laborers can be replaced with robots. Robotics and artificial intelligence can be incorporated into the vehicles and machineries, enabling them to start the engine, steer the vehicle or machine, accelerate, slow down, apply brakes, drill through the surface, mine for coal, and more, all on their own without any remote assistance.
These vehicles or machines can also carry out very specific jobs, such as blade control and dump bed control. Although these are much costlier to procure, they offer a huge boost to productivity since human control is eliminated. In addition, there is absolutely no need to be behind the controls all the time tracking and triggering every little move and shift. It is, however, important to note that, even though fully automated vehicles and machines can eliminate the need for numerous labor workers, you would still need to hire mining facilitators and troubleshooting experts, who can deal with any technical errors that come up in the machine or vehicle.
Automation in Software

Planning Mine Layouts
A coal mining field is an incredibly dangerous and a risky place to be at. You need to be on your toes every second and have to make sure that you aren’t digging in high risk areas, where the ground underneath can cave in or sink. If it were to happen, it can lead to not just a waste of effort, resources, and capital, but also the loss of many lives of the miners working in the field. Mining software has helped to automate the process of designing layouts and putting vertical lifts, and blasts in appropriate locations.
It uses technology to automatically detect the stress levels in the numerous layers of the ground, thus allowing you to set up planned and strategic locations. The loss of effort, resources, capital, and human lives can therefore be reduced to a minimum, and you do not have to spend a lot of time figuring out where you can install a particular thing.
Analyzing the Stability of Pillars, Seams, and More
There are several structures that need to be installed when you conduct mining. These include longwall pillars, multiple seams, roof bolt systems, retreat mining pillars, and more. The stability and strength of these structures are of paramount importance, and no part of their design or layout can be overlooked or compromised with. There have been numerous previous cases where people have lost their lives or have had to deal with severe injuries and even permanent damages such as paralysis at times when one of these structures gave away or wasn’t stable enough to sustain.
Automation solutions have allowed miners and engineers to have faith in such structures since the software can automatically analyse the stability of these structures. If they are unstable, the software will prompt a warning asking you to make necessary changes to sustain the structures. These solutions are low cost and quite affordable. They are also incredibly easy to use and can provide quick results, thus reducing the tremendous amount of time, which was previously spent on manually checking the strength and stability of the structure.
Large datasets have to be evaluated at high speed to prove the economic viability of the structures. In addition, these structures are incredibly expensive to install. A longwall pillar could take anywhere from $60 million dollars and more to install. Even the slightest issue could cause the loss of a truckload of money. Once the geological area is assessed, the software can provide 3D models for the structural interpretation.
Surface Mining Automation Software
Not all mining is done underground, and the layout designs for surface mining can be obtained using automation solutions as well. These software don’t just recommend layout plans, but also test them in plan, section, and 3D views. This allows them to make sure that all the corners are covered and no high risk areas are being overlooked when preparing the design. This automation in geological and surface coal mining has allowed miners and engineers to navigate through some extremely difficult terrains with a lot of ease.
Engineering and Scheduling Model
This automation tool examines the extent of deposits in the ground and calculates how much ore can be mined. A geological model is analysed, which then provides information on mineable and non-mineable coal deposits in the area. In this way, miners and engineers no longer have to keep digging in a place for months and end up with very little to no ores.
The next comes a scheduling model, which examines the sustainability of the digging patterns suggested by the engineering model. It also determines the rate and quantity of digging or mining required. This is a smart tool that takes care of all high stress points that are currently present on the ground or likely to develop in the near future. It also provides recommendations on altering the current parameters to continue a steady stream of mining in a particular area. This allows miners and engineers to make sure that there are no gaps in the plan ahead and the operations aren’t affected too much.
Advantages of Emerging Automation

Better Safety
One obvious and the most important advantage of automations in the coal mining industry is improved and better safety of all workers involved in every process. They no longer have to take a huge risk on their lives when going underground for mining. Much more stable and strong structures, which have undergone thorough testing before being put up in the location, are built. Moreover, remote and teleoperated machines allow miners and engineers to get the desired amount of coal they want without being in close proximity to the mines or caves. Thus, even if there is an unforeseen and sudden accident where the mine caves in or sinks or a structure falls down no lives will be harmed.
Environmentally Sustainable
Numerous previous mining projects that were undertaken yielded not so great results, but they sure utilized loads of environmental resources, such as energy, water, and wood. This has and continues to impact the environment heavily. Thus, social and governmental regulations began to be introduced to make sure that mining companies weren’t exploiting the environmental resources. This led to the depletion of throughput in mining companies since they didn’t have the required tools and technologies to use resources sustainably.
Reduced Fatigue in Drivers
Mining is an incredibly energy draining job, especially for drivers. With loads of automation coming into play with respect to the drills and vehicles, drivers can take a breath of respite and relax. Drivers no longer have to navigate through rough terrains without being aware of what they might have to tackle next. They are highly informed about what lies ahead, and they can easily drive without putting too much effort or worrying about the statistics of things.
Improved Working Conditions
Now that numerous mining operations can be taken care of without having to be in close proximity to the coal caves and deposits, especially underground mines, working conditions have improved incredibly. Most processes and operations are carried out from a distance, thus reducing the chances of health ailments such as asthma and bronchitis to a minimum. Workers are also safe from physical harm, such as fractures, wounds, or even permanent damage such as paralysis. Automation of numerous processes has reduced the chances of deaths in coal mines by a large extent.
Less Occurrences of Unscheduled Maintenance
Sophisticated automation tools are incredibly good at what they do and rarely fail. They also alert engineers when a system or machine is about to go bust and needs immediate maintenance. Previously, there used to be loads of occurrences of unscheduled maintenance since engineers had no idea what was working and what wasn’t. With such sophisticated machinery and processes, the occurrences of unscheduled maintenance have reduced a lot. This is because these tools allow the scheduled work to be carried on as usual without any unforeseen delays or hindrances.
Better Fuel and Energy Efficiency
All machines, drills, and vehicles in a coal mine operate on either fuel or energy. When operations and processes are well scheduled, planned, tried, and tested, fuel and energy are used in a highly practical and an efficient manner. There is no wastage of fuel and energy on processes that are later deemed useless or redundant. This allows better resource maintenance without impacting the environment much.
Drawbacks of Automation
The biggest drawback of introducing automations in the coal mining industry is the loss of numerous jobs. Miners are usually workers from marginalized or underprivileged communities who do not have any other job opportunities available to them. When automated tools take their places, they have nowhere to get livelihood from. Another problem is that, even though a lot of research is going on regarding these automations, there aren’t enough stakeholders who are willing to test out things in real coal mines.