Choosing the Right Drilling Technique for Natural Gas
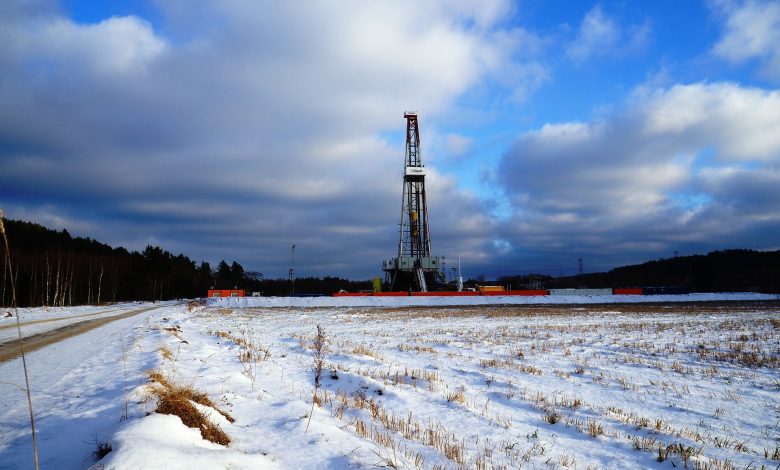
Natural gas can be found around us everywhere. When you return home from a long day at work and turn on the stove to cook some food, you’re making use of natural gas. Natural gas is used for several other purposes – including heating our homes and powering our cars and buses. This may have you wondering, how is natural gas obtained? Well, here is a brief explanation as to how natural gas drilling works.
Like locating and drilling for any other form of energy, the process for drilling natural gas begins with the usage of a variety of methods to identify and locate natural gas resources deep beneath the Earth’s surface. For starters, experts look at the surface geology of an area, the flow of seismic energy from inside the Earth to its surface, as well as the magnetic properties associated with underground rock formations. Once a deposit of natural gas is located, energy companies use drilling techniques to obtain the natural gas.
Natural gas is often stored in a well, and these wells are dissimilar to water wells, which are known to fill up with water upon drilling. Natural gas is contained within the underground rock mass where it is first located, and the same rock must be broken in order to release the natural gas inside it. Energy companies will first drill a hole, and then line the hole with certain materials that will retain the gas within the hole. After this step, electric charges are released into the well and this affects the rock formation where the gas is trapped. A highly-pressurized liquid fracking solution is then released into the well, and this liquid is responsible for breaking up the rock completely, and thereby releasing the gas. As the gas weighs lesser than the fracking solution, it rises to the top and gets released. The entire process has to be carried out very meticulously and carefully, as any step in the wrong direction can release this natural gas into the groundwater.
While this is the most widely practiced technique for obtaining natural gas, it has been met with quite a few controversies. The people who suspect the technique believe that this process releases dangerous chemicals into the groundwater, thereby contaminating tap water and also affecting agricultural water supplies. Additionally, the fracking solution also contains several toxic chemicals, and when left behind, it can merge with the groundwater, causing further problems.

History of Natural Gas Drilling
Natural gas has been used since ancient times, yet the commercial extraction of this gas is quite recent. The history of natural gas dates back to 1000 B.C., when the famous Oracle at Delphi, located on Mount Parnassus in ancient Greece, was built at the location where natural gas reached the surface in a flame. Later on, in 500 B.C., the Chinese population began to use bamboo ‘pipelines’ in order to transport gas that reached the surface, and used it as energy to boil the sea water to make it consumable for drinking.
The first known commercial use of natural gas dates back to the year 1785. The British used natural gas obtained from coal as a source of power to light their houses and streets. Almost 30 years later, in 1816, the city of Baltimore in Maryland became the first American city to use this type of manufactured natural gas to power their street lights.
In the United States alone, naturally occurring gas was first discovered as early as 1626 when the French explorers found Native American people lighting up gases that were seeping into and around Lake Erie. The first natural gas well was first dug in Fredonia, New York, which also led to the formation of the Fredonia Light Gas Company, America’s first natural gas distribution establishment.
While the 19th century witnessed natural gas being used exclusively as a source of light, the year 1885 became a turning point in history. Robert Bunsen invented what is known today as the Bunsen burner, and this opened up several new opportunities for the use of natural gas. The invention led to the establishment of effective pipelines in the 20th century, and soon the use of natural gas expanded to home heating, as well as cooking. Water heaters, oven ranges, manufacturing plants, and even boilers began to use natural gas to generate electricity.
The Status of Natural Gas Today
As of today, natural gas plays a very important role in the world’s supply of energy. More than one-half of the energy consumed by residential and commercial populace and 41 percent of the energy used by the U.S. industry is supplied by natural gas. Today, natural gas is known as one of the cleanest, safest, and most versatile forms of all energy sources.
Almost 99 percent of the total natural gas consumed in the United States comes from natural gas supplies in North America. Natural gas also makes for one of the most environmentally-friendly sources of energy, as it is the cleanest burning fossil fuel available to us. Aside from propagating a cleaner and greener environment, natural gas also allows for enhanced energy security and a more competitive economy.

Different Types of Drilling
Percussion Drilling
Percussion drilling is also called as cable drilling, and this technique is carried out by attaching a hammering unit to a cable, which is then lowered into the hole. The drilling technique is a manual one, and the driller often uses a tripod to support all the equipment. The technique uses a back-and-forth motion, which helps to loosen up the soil in the borehole, after which extraction is carried out with the help of a bailer. At certain intervals during the process, the hammering bit is removed, while the cuttings are suspended in water, and later removed by pumping water to the surface. The equipment is covered with a steel casing, and this helps to prevent the hole from collapsing during the process. The casing also prevents the elements from contaminating the groundwater in the area. The temporary setting is later removed after a permanent screen and casing have been installed. With this technique, manual percussion can reach about 25 meters underground.
Percussion drilling is ideal for both unconsolidated and consolidated formations, which include sand, silt, sandstone, and sometimes even gravel.
Rotary Drilling
Rotary drilling is yet another common drilling method which is used to dig up exploratory and production wells, and this method of drilling can penetrate over five miles of underground depth.
With this method, lightweight drills are used to drill low-depth wells, and then rotary mobile and floating drills of differing sizes are used to dig the exploration wells. First, the equipment is mounted atop a platform which holds a 40m high derrick, as well as a rotary table, handy engine, mud mixer, and injector pump. The equipment also consists of a winch and 27m long pipe sections that are used for the drilling process. The rotary table directs the square Kelly that is connected to the drilling pipe, and the mud swivel attached to the pipe is connected with blowout preventers. The pipe rotates at a velocity of 40 to 250 rpm, and the drag bits, sharp cutting edges and rolling cutters with strong teeth, effectively drills open the ground.
The cuttings are then removed with the help of a fluid circulation inside the pipe. Air-based drilling methods allow the drill to penetrate faster, and these are much more efficient as compared to the water-based drilling techniques. The drag bit is especially useful, as it allows for the penetration of unconsolidated sediments, and this later allows the roller bit to drill through the consolidated rock formation. Depending on the hardness of the formation material, the drill rotation speed can be adjusted to suit the process.
Dual-Wall Reverse-Circulation Drilling
The dual-wall reverse-circulation drilling technique uses two concentric drill pipes to create a more controlled flow. First, the drilling fluid is pumped with the help of an outer swivel that reaches the bottom of the bit, which then ricochets upward to the main pipe. All the cuttings of the formation are carried upwards with the help of an internal pipe and a surface swivel. The method is applicable for all types of geologic formations, without the need for a surface casing. An advantage presented with this technique is that it is compatible with both rotary drilling and percussion drilling methods. The method allows for all the fluid to be circulated within a controlled space, and the recovery of cuttings are also made easier.
The dual-wall reverse-circulation technique allows for geologic sample collection, wherein the samples are delivered through the cyclone created at the surface point of drilling. One of the main strengths of this method is good sample recovery. The technique also makes way for fast penetration in alluvial and fissured rock formations. Moreover, the method helps to deliver an accurate estimate of aquifer yield from the formation.
Electro Drilling
With this method, rotary tables and winches are driven with the help of electric motors, which allow for greater flexibility of remote-controlled operations. Electro drilling is comparatively new to the science of oil and gas exploration, and this technique is credited for providing more direct power to the drill bit by connecting the motor above the bit and underneath the hole. One of the primary merits associated with electro drilling is that it performs well in complex geological conditions where the use of weighted mud or mud mixtures are prevalent. Electro drilling also allows for more savings in energy and material usage, due to which this technique is widely used in areas like Turkmenistan, Azerbaijan, and Ukraine.
Electro drilling combines the merits of rotary and hydraulic-motor methods, and thereby offers a wide range in drill-bit rotational speeds. Yet another advantage of electro drilling is that it uses different borehole cleaning agents and can also offer controlled drilling of deviated boreholes.

Directional Drilling
Directional drilling is similar to rotary drilling but uses certain advanced techniques as well. With this drilling method, drillers can access curved paths and further deepen the hole. Directional drilling allows for oil explorers to reach the areas that cannot be easily accessed with vertical drilling. Directional drilling allows drillers to access several wells, all in different directions, with just a single platform. The technique is highly preferred to tap into undersea reservoirs, and with the help of computers, one can guide the automatic drilling equipment without the need to connect and disconnect sections during the process. One of the major advantages of this technique is that it is highly cost-effective, and this makes it one of more preferred drilling options of today.
Horizontal Drilling
With this technique, a vertical well is first created, and then the drilling equipment turns horizontal within the reservoir rock in order to expose more of the open hole. The technique uses horizontal ‘legs’ that can extend over a mile in length. Increased length will allow for more oil and natural gas to be drained, and also improve the rate of flow. An advantage of this technique is that more natural gas can be produced with fewer wells, as well as a limited surface disturbance. One drawback of this technique is that it can be used only on certain specific surfaces.
Multilateral Drilling
Multilateral drilling, as the name suggests, allows drillers to access oil and natural gas reserves that are located in separated layers underground. Natural gas explorers can easily branch out from the main well to tap into reserves that are located at different depths. The primary advantage of this technique is that it allows for increased production of natural gas from one single well, and also reduces the overall number of wells that have to be drilled on the surface.
Extended Reach Drilling
Sometimes, certain environmentally-sensitive or underdeveloped areas cannot be accessed for vertical drilling purposes. With extended reach drilling, producers can reach the deposits that are located over five miles from the actual place of drilling. The technique is used for offshore drilling, as this method allows producers to reach deposits located in far off distances, thereby reducing the total number of platforms required to produce the natural gas, and also reducing the overall surface impacts.
Complex Path Drilling
Complex path drilling allows natural gas explorers to create well paths that contain several twists and turns, and this helps them access multiple accumulations from just a single well location. A primary advantage associated with complex path drilling is the reduction in overall expenditure, as well as minimization of waste production and surface impacts that arise from drilling multiple wells.

Developing the Site for Producing Oil and Natural Gas
Contractors have to undertake extensive site development in order to bring a new oil or gas field to production. In some areas, the access to the site is limited due to certain climatic and geographic conditions, and contractors have to take extra precaution in setting up the equipment in these areas. The requirements to be undertaken by contactors include – construction, maintenance, administrative activities, housing, oil, gas, and water separation equipment, transportation for crude oil and natural gas, waste disposal facilities, and several other equipment and facilities. Oil and natural gas depository sites are often not equipped to handle such equipment, and it becomes the contractor’s responsibility to oversee all the drilling requirements as suited to a particular area.
Environmental Concerns with Drilling
Oil and natural gas production contribute significantly to environmental pollution. Air, water, and ground pollution is prevalent wherever drilling activities take place, and this has brought about the need to employ environmental conservation efforts with every single process. Most of the pollution caused by drilling are from oil spills, gas leaks on land and sea, hydrogen sulphide from gas escaping into the atmosphere, dangerous chemicals seeping into land and water, and combustion of oil wells. The oil well fires that occurred in Kuwait during the Persian Gulf War in 1991 have brought to the notice of authorities the potential public health effects that arise from these large-scale fires.
Here are some of the pollution control measures that are currently being employed by authorities responsible for drilling:
- The utilization of API separators and the inclusion of other waster and water treatment facilities is being done.
- Spill control measures are being employed to overlook leakage of hazardous material into the sea or groundwater.
- In case of a spill, containment measures are undertaken, and drainage is carried out to control oil spills and divert the oily water to treatment facilities.
- In terms of research, a gas dispersion model is being constructed, which will help to ascertain the areas that could be affected by a cloud of toxic or flammable gas that could escape during the process. Groundwater table studies are also being carried out to understand the extent of oil contamination that can occur in water.
- Lastly, the authorities have paid special attention to the training and qualification exercises that are to be undertaken by workers. Contractors are also made aware of pollution remediation efforts, and training for the same is also made mandatory.

Based on the location of the natural gas depository sites, the producer of natural gas will have to employ a suitable drilling technique to access the gas, with minimal resources and reduced wastage. With the help of automated technology, the drilling process is set to become easier and more accessible.